Collaborative robots have completely changed the way companies approach automation. Instead of dedicating huge capital outlays to acquiring bulky robotic systems that will replace their employees, companies now see automation as a collaborative approach. One where robots are merely tools aimed at optimizing the productivity of their employees and this has gone a long way towards increasing the odds of frictionless deployments.
One of the things that have made it possible for employees to work alongside cobots is the fact that these robots are incredibly safer. They come with superior technologies that allow operators to control how and when to execute the tasks that they are assigned. The following are the different ways in which a robot can be made even safer by simply focusing or making changes to its arm.
One thing is for sure – this will change the industry we know in so many ways. Some job positions will be replaced with these automated machines. But, at the same time, it’s safer for the risky positions, especially in the industry and manufacturing process. According to universal-robots, People don’t need to be near the machines, because they can control them from a distance, which leads us to the conclusion from the topic, that robot arms are indeed safer to use, so the human lives can be saved, and not put at risk in any way.
Now, let’s see how it’s done, and what are the benefits of automation and robotic approach in the factories:
1. Reducing the speed with which it operates
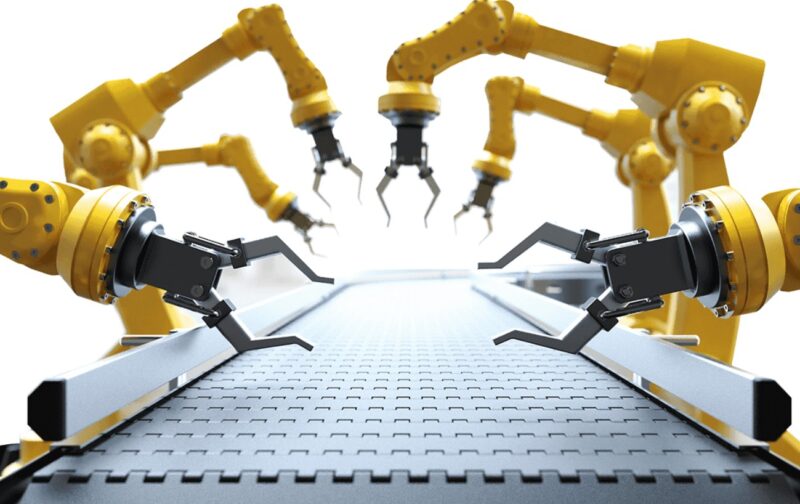
Robotic systems work faster than human beings, and this is the main benefit of the automation process. In the production line, you can even increase their speed without sacrificing the accuracy with which they operate, which is great for your profit. However, if they are working alongside human workers, it is usually impossible for the human worker to keep up with the speed at which the robot operates. This is something that will increase the risks of accidents and injuries simply because the two are not in sync. Humans can’t be really replaced in this case, but they can be moved away from the risks until the machine is done. Then, they can go to give the complete human touch to the process, and that’s why the machines and people will work together for a long time.
You can make your workplace safer for human workers by reducing the speed with which the cobot’s robot arm moves. Doing this will reduce the risks of the workers making mistakes that may ruin your business. It will also allow the human to be able to track the movement of the cobot and hence get out of the way in case something goes wrong. As a result, reducing the speed at which your robot operates can go a long way towards reducing accidents, injuries, and cases of property damage in the production line. This approach may have many ethical issues, but as soon as lives are not put at risk, everything is allowed.
2. Reducing the force with which the robot arm operates
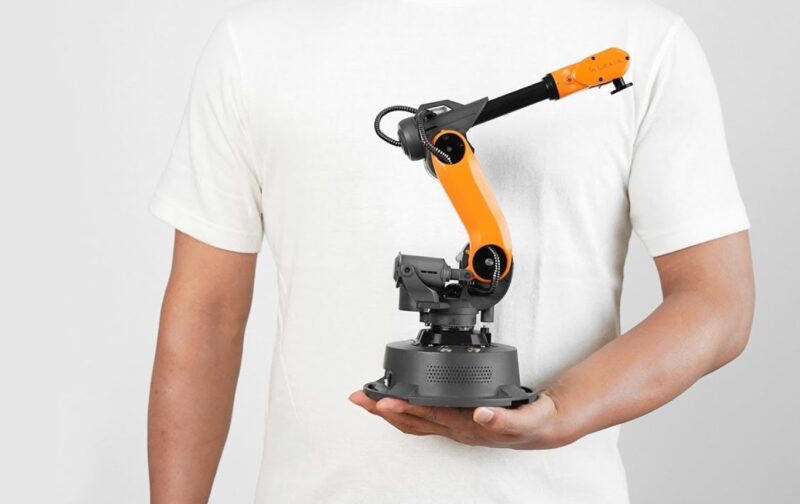
While reducing the force with which the robotic system operates will not reduce incidences of mistakes or accidents, it will reduce the severity of the injuries or damage that results from such mistakes. Essentially, by reducing the effective force of the robot arm, you guarantee that if the employee accidentally ends up in contact with the arm, the impact of the arm won’t be as catastrophic as if the arm were moving at full force.
It is important to note that this is an adjustment that isn’t always possible for every application since some applications require the robot to operate with a high degree of force at all times. In such a case, you can consider having robots collaborate with each other on these tasks, and then assigning your employees tasks that featureless risk of injury.
3. Fitting your robots with motion and vision sensors
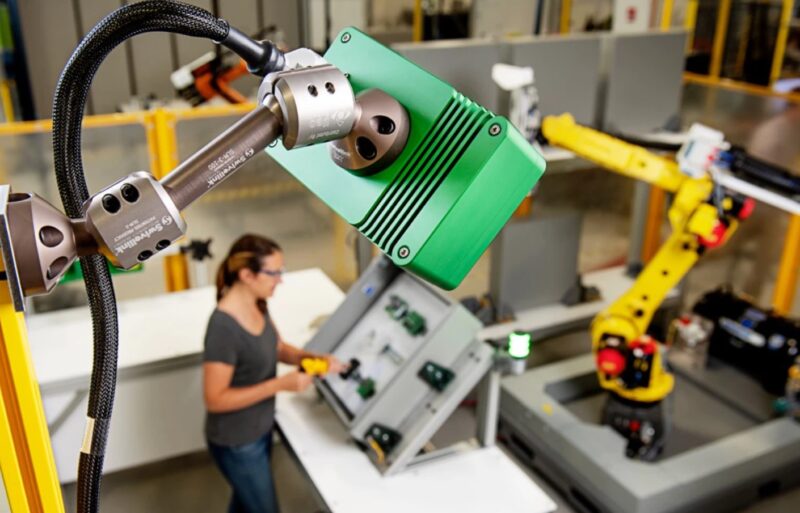
Sometimes, changing the speed or the force with which a robot operates is not an option. This may be due to the nature of the task that the robot is executing. It may also be due to productivity optimization demands. Whichever the case, you can still make it safer for your employees by simply fitting the robot with additional sensors.
Motion and vision sensors help robots to better understand their environment. Therefore, by fitting your robot with the right sensors, you can enable it to detect when a human being is within its vicinity. As a result, you can program the robot to completely stop, reduce the speed with which it is operating, or even reduce the force with which it moves its arms. And since the robot will be able to do this automatically and with incredible accuracy, it may even be unnecessary to have restricted zones or safety rails and cages on your production floor.
When you consider how easy it is to make the operation of these robots safer, their affordability, and the fact that they take up less space, it is easy to see why small and medium-sized companies are increasingly choosing them as their automation solutions.
Technology, in general, brings a lot of benefits in almost every aspect of our life. Using the robots and robotic arms and joints in the manufacturing processes and production lines in the industry is often a discussion topic because it’s practical, but at the same time, it reduces the need for workers and may lead to closing so many job positions.
The technician who will control the whole process often needs to have a degree in electrical or mechanical engineering, system engineering, and automation. Robotics courses may be an additional benefit. On the other hand, the industry opens a lot of job positions for engineers, and at the same time, closes general workers positions. But, chances are there to be embraced, and there is nothing wrong if the company owner wants to incorporate the robotics technology in the production lines.
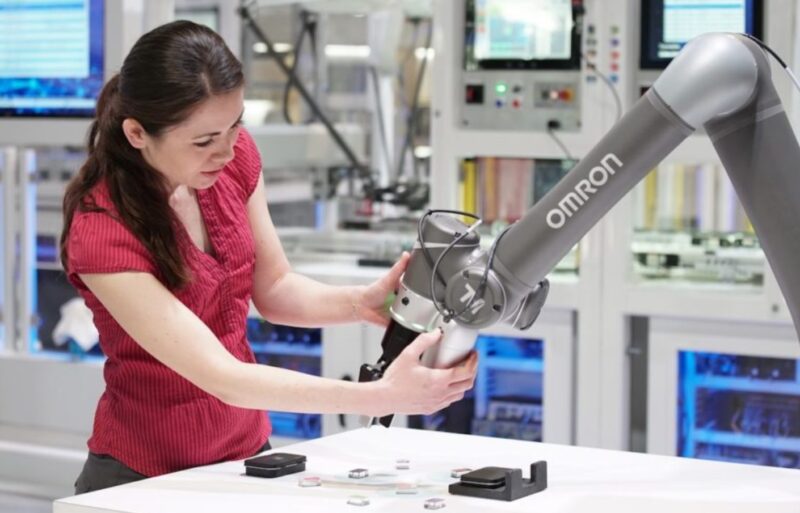
As a conclusion to this topic, we can say that robotics and automation are getting even better and more independent as the years go by. The industry should embrace these technologies if the company wants and needs to stay competitive in the market. Probably there will always be ethical issues that we must overcome, knowing that the technology will be able to replace a whole department of people.
So, if you are looking for a career, you can consider studying mechanical or electrical engineering. These professions are highly demanded in the industry, and surely you can be a robotics designer or controller, which is really great, taking in mind all the things we described in this article.