Every year, technology never fails to surprise humankind. With new tech releases from different industries, people are barely keeping up with the pace of technological advancement.
As necessities and demands increase day by day, manufacturers and product creators face the challenges of speeding up their production, lessening material waste, reducing human error, and improving quality. Thankfully, 3D printing is here to save the day.
It doesn’t take a tech expert to explore the wonders of 3D printing. In this article, you’ll learn what 3D printing is all about, including its humble beginnings, equipment and materials utilized, and the 3D printing process steps.
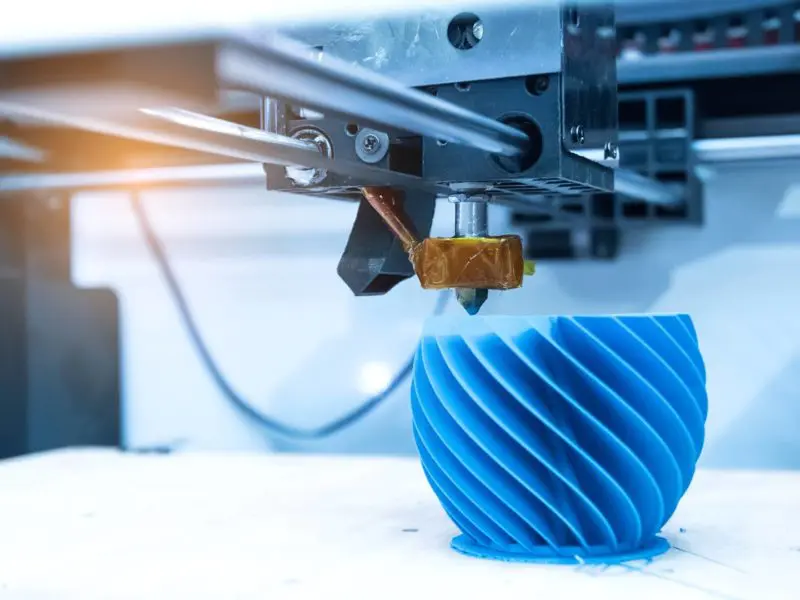
3D Printing: From FILE To LIFE
Three-dimensional (3D) printing is a manufacturing practice of transforming 3D models from a digital file into real-life 3D objects. To put it simply, it’s like printing on paper, but your end-product features a 3D object instead of a 2D one.
3D printing is also called additive manufacturing as one can use additive processes, such as stacking up multiple layers of material to create a 3D item. Imagine completing a puzzle, as each puzzle piece signifies a layer, and all these pieces will form into a 3D structure.
Because of the numerous benefits of utilizing 3D printing technology in different industries, integrating 3D printing into businesses that involve products and goods is worth considering. If you’re planning to do this, look for the best 3D printing services, like jawstec.com, and ask for printing capabilities and quotes first.
3D printing was first imagined in 1981 by Hideo Kodama through a rapid prototyping technique. He modeled a photosensitive resin and used ultraviolet (UV) light to polymerize it. In 2009, the closest technology to 3D printing emerged, known as fused deposition modeling (FDM), which works like an extrusion that deposits plastic filaments plastics following a 3D pattern.
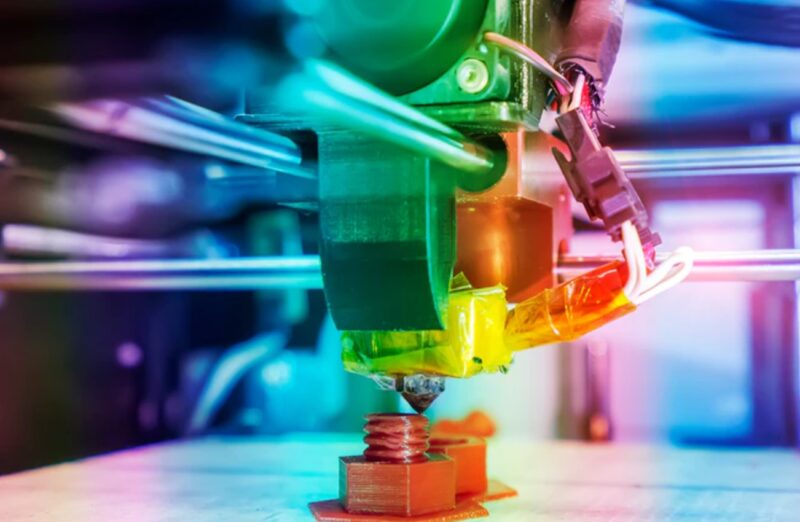
Instruments That Make 3D Printing Happen
Additive manufacturing has various products and applications, and it’s not a surprise that you can use a diverse range of materials to create a 3D-printed object. Case in point, manufacturers use different materials to make 3D-printed tissues and organoids versus 3D-printed automotive components.
Essentially, it would be impossible to 3D-print an object without the following tools and instruments:
- 3D Printer: Ordinary 3D printers are similar to inkjet and laser printers, except that they use a different type of ink. While they’re typically used in manufacturing and production, they can also be bought for personal use.
- 3D Printer ‘Ink’: A 3D printer can’t construct a 3D-printed product without any installed ‘ink,’ or in the 3D printing world, called filaments. While inkjet printers use ink and laser printers use powder, you can’t build a 3D-printed product with these materials alone.
3D printers use thermoplastics that melt with heat and cool down after 3D printing, which you’ll discover later on. The most common plastic loaded in 3D printers is acrylonitrile butadiene styrene (ABS), often seen in LEGO ® bricks, plastic computer parts, and refrigerator components.
ABS is an ideal 3D printer ink because it’s chemically combined from butadiene styrene (synthetic rubber component) and acrylonitrile (rigid plastic component). It can melt without extreme heat and return solid at room temperature, and it doesn’t melt under the sun.
Meanwhile, 3D printing applications in the medical industry use different ink types when printing tissues and organs. Instead of thermoplastics, 3D printers used in biomedical advancements utilize biomaterials composed of living cells, skin tissues, or blood vessels.
- 3D Modeling Software: When someone mentions 3D printing, the first thing that people associate with it is a computer-aided design (CAD). Before ending up with the 3D-printed end-product, you should initially have the 3D model that the 3D printer will follow.
By using CAD software, one can design and develop their desired 3D object. CAD software programs offer features and functions, such as drawing creation, parametric modeling, design automation, stress analysis, which allow designers to visualize their models better.
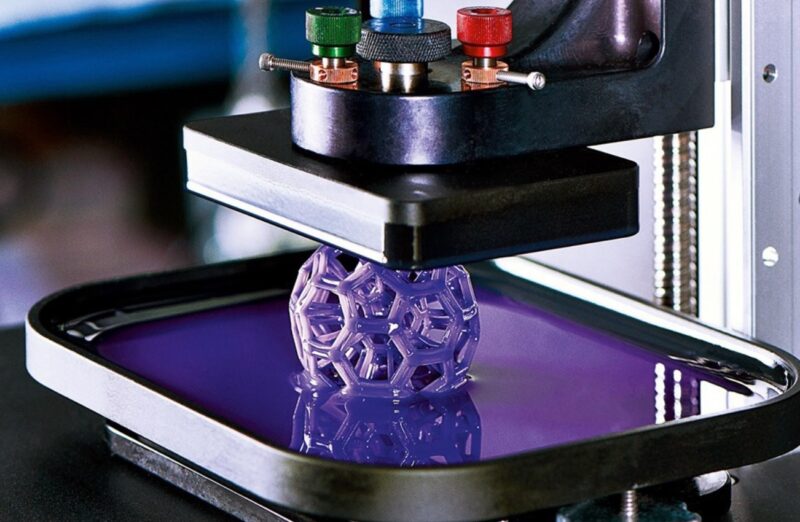
The 3D Printing Process
Moving onto the highlight of 3D printing is the actual steps of the said process. Unlike traditional printers that automatically print documents in one click, 3D printing has the following steps to make the process more efficient and reliable:
- 3D Modeling: In the 3D modeling step, designers use a computer-aided (CAD) application mentioned previously to create 3D models of the desired product. Unlike the old ways, which involve sketching on paper, designers can better represent their models with features that manual drawing can’t accomplish.
Aside from modeling the product themselves, creators may opt for 3D scanning, which scans a real-life object and instantly generates a digital replica of it. This scanned 3D model can also be configured and modified before 3D printing using the said CAD software.
Lastly, there are also paid 3D downloadables online that have already been modeled by other users. After downloading, you can immediately proceed to the next step or experiment with the downloaded 3D model.
- 3D Slicing: You can’t print the 3D model directly after the designing step as the printer can’t process the complexity of raw 3D models. Therefore, the model must undergo the slicing process by translating the 3D model into instructions that the 3D printer can understand. Typically, 3D model slicing involves chopping and dividing the model into layers, then printed by the 3D printer step-by-step.
- 3D Printing: For the actual 3D printing, the 3D printer will then extrude the thermoplastic material and start moving according to the instructions set on the slicing step, thus forming the 3D-printed object. You don’t have to worry about the thermoplastic being melted as ABS plastic can quickly cool down.
- Finishing And Polishing: Last, but not the least, is the finalization process of the 3D-printed product. The finishing and polishing actions will differ depending on the desired product. This step may include polishing, painting, sanding, assembling, and other post-processing methods.
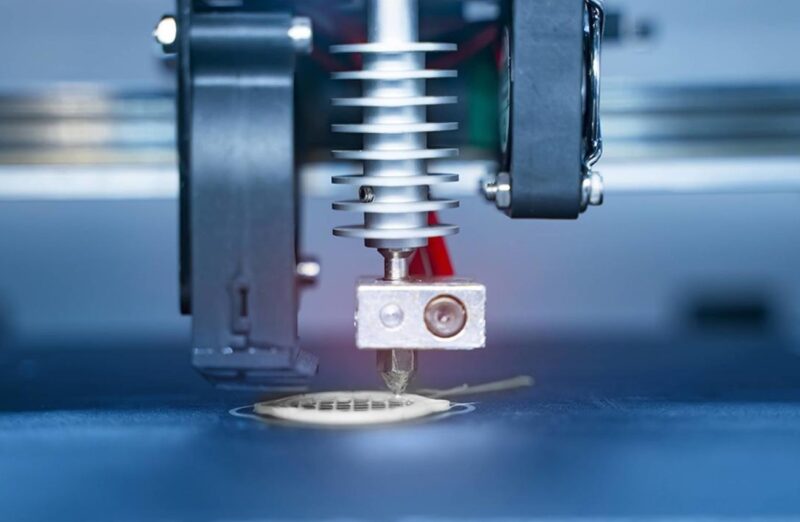
Bottom Line
There’s no doubt that 3D printing has changed the manufacturing industry. As 3D printing becomes more readily accessible to companies and individuals, it’s only a matter of time before it transforms into a mainstream technology. As long as 3D printing enthusiasts and creators understand what 3D printing is all about and use this piece of technology productively without bad intentions, humanity has nothing to worry about.