The manufacturing process is the foundation of any product you plan to sell, so everything about your process must be as efficient as possible. This includes everything from deciding what order to follow to assemble the parts and which tools to use during production. If you want your manufacturing process to succeed, follow these simple ways to optimize every step.
1. Embrace Technology
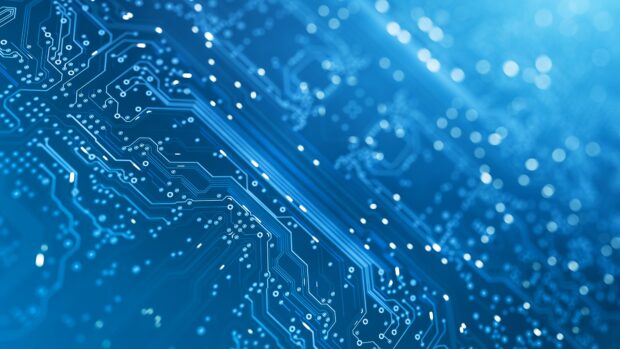
Using cutting-edge technology allows manufacturers to improve their production line by creating more efficient workflow procedures, completely automated facilities, and even greater inventory management systems.
According to Sculpteo, making use of 3D printing is a great way to streamline your manufacturing process. One of the most popular uses of 3D Printing is prototyping. However, it can also be used for production purposes. 3D Printing speeds up the prototyping process and saves time and money compared to traditional prototyping techniques such as machining.
3D printers make complex shapes and feasible designs that would normally require a mold to create. 3D Printing allows you to 3D print ten test parts for every part machined, making 3D Printing a perfect optimization for your manufacturing process.
Other technology, such as robotics and computerized design software, allows companies to create products from start to finish without having employees all across different areas of the company coming together to make one product.
2. Inventory Management Is Crucial
When it comes to having an efficient manufacturing process, inventory management is key. First, manufacturers need to understand what they produce in terms of quantities and when these products require new parts.
This allows the manufacturer to make plans for future production runs without excess inventory accumulating. Furthermore, accurate inventory records keep track of potential malfunctions, allowing for prompt repair. Finally, having the right amount of inventory reduces unnecessary costs associated with storing parts and raw materials.
3. Improve Supply Chain
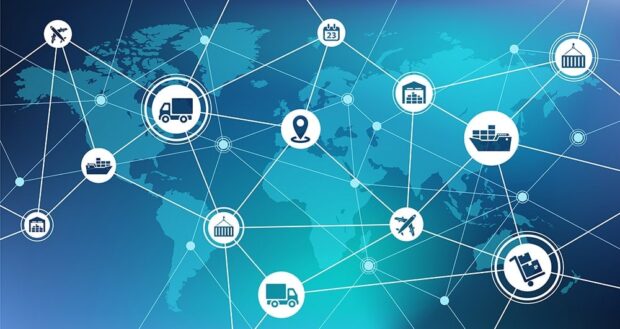
Manufacturers need to employ a system that allows all suppliers to work together efficiently, along with distributors and retailers. Consistent communication between these groups is necessary so the product can be made and shipped on time. The supply chain should be streamlined so there are no hiccups in production due to part shortages or closed factories.
4. Set Standard Operating Procedures
While many manufacturers already have standard operating procedures, it’s important to re-evaluate these guidelines and update them as needed. SOPs should be detailed enough for factories to function properly without much oversight and flexible enough to easily change as the product evolves.
5. Learn From Mistakes
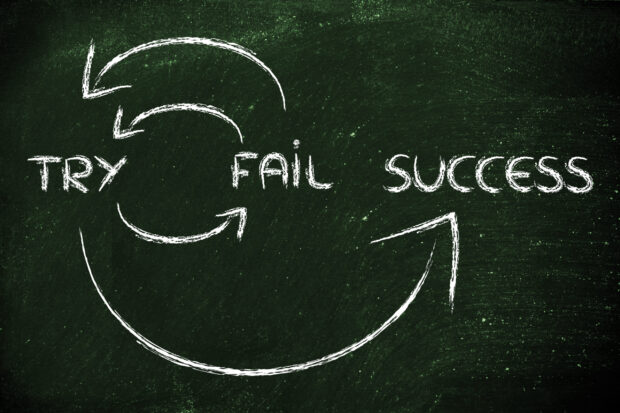
There will always be manufacturing problems, but it’s how these issues are handled that matters most.
It’s crucial to document each production mishap thoroughly in detail, so no one makes the same errors again in the future. Learning from mistakes ensures that products are of high quality and continues the production process effectively.
6. Increase Process Awareness
Manufacturers need to understand how their operations work and what they do well. Identifying the strengths of each process will allow for improvements based on those areas where efficiencies are lacking. By taking the time to understand each process, manufacturers can make improvements that create a more efficient workflow for all aspects of production.
7. Improve Scheduling
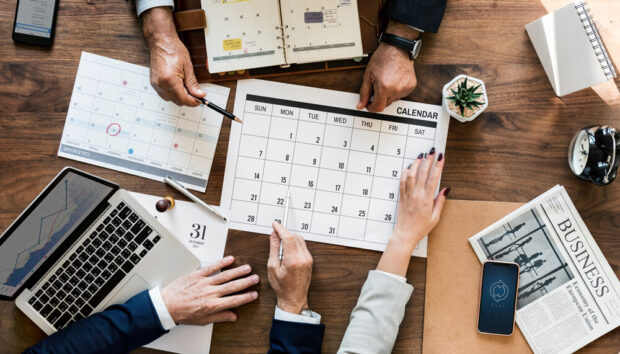
Schedules should be created with multiple factors in mind, including a budget, timeframe, and quality expectations. Key performance indicators (KPIs) help companies track their manufacturing processes and identify areas where they need to improve efficiency. Once these areas are identified, companies can create better schedules that allow time for problem-solving without pushing deadlines back.
8. Require Quality Checks
Quality checks are a crucial part of the production process because they ensure that the products being created meet the standards set by the management. This step helps manufacturers discover problems early while also preventing defective items from reaching consumers. When quality checks are required for each production stage, companies have more control over final product quality and can prevent low-quality goods from being sold to consumers.
9. Use Lean Manufacturing Resources
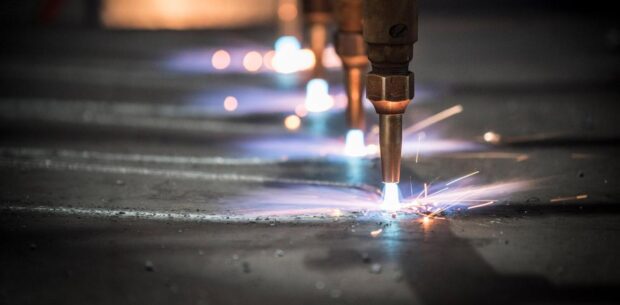
Lean manufacturing is an important part of streamlining any kind of company’s supply chain or production line. It only focuses on doing the necessary things without wasting time or money. Lean manufacturing focuses on identifying areas where the company can make cuts, whether in the form of inventory or excess staff members.
It’s important to note that lean manufacturing doesn’t necessarily cut costs; it only identifies what processes aren’t working and allows changes to be made without straining budgets.
10. Use Production Simulation
Production simulation is a great tool for companies with outdated systems that can no longer keep up with current market demands. These systems allow manufacturers to simulate real-world production situations so they can identify areas of improvement before actually making changes to their actual workflow procedures. This allows them to discover inefficiencies before they happen instead of after the fact.
11. Outsource Production Tasks
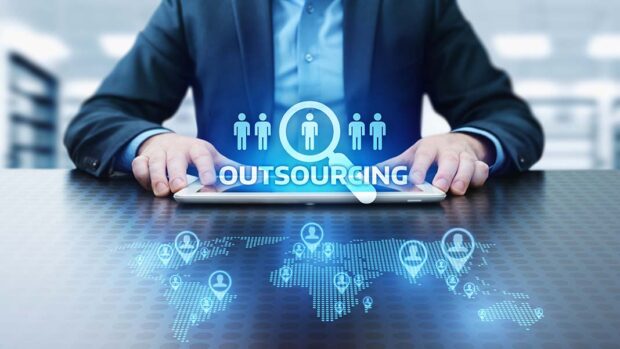
Outsourcing specific tasks and processes is a good way for manufacturers to reduce costs and increase production efficiency. By outsourcing one or two aspects of production that aren’t core competencies, businesses can save money by hiring contractors rather than full-time employees; this frees up time and resources that can be used elsewhere.
This strategy also opens up opportunities for manufacturers to expand their market reach. For example, if a manufacturing firm outsources packaging but keeps assembly internally, it has opened itself up to potential new customers who only want one particular part of the process completed.
12. Monitor & Predict Trends
By keeping an eye on the trends in your industry, you can see what’s popular with consumers and how each new product is being used overall. By using this data while also looking at feedback from consumers directly, you can create the perfect marketing strategy that will help increase sales over time. Try to keep up with changes in consumer behavior so that trends won’t be missed or taken advantage of too late – by doing so, you could gain significant ground over many competitors within your market.
13. Find Ways To Reduce & Recycle Waste
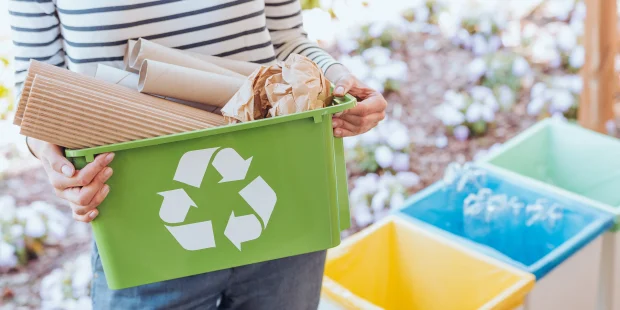
Every last part of a production process should be looked at to see if there are any ways it could be done more efficiently while also reducing the amount of waste produced in some way. Depending on what company you work for, there might even be an opportunity to recycle your waste material or share these resources with other employees in your organization who need them. This will, once again, save you money in both the short term and long term, which can help bolster your overall budget considerably.
Conclusion
These are just some tips to help improve the efficiency of your manufacturing process so that everything runs much smoother than it does now. By following these suggestions, you should see noticeable improvements in your process. As with everything else, the key is always to research as deeply as you can so you know what your specific production process needs.