Since the early days of the industrial revolution, there have been concerns about the need for human employees. This has been a problem for almost every society throughout history. The earliest examples started with the ancient Greeks. Perhaps, they didn’t have to worry about getting help from services like assignmentgeek.com, but the problem has quite a long history.
The cotton gin eliminated the need for many cotton spinners in the mid1800’s and significantly increased production. In the 1900’s many farmers were replaced by tractors. In the 1960s machines replaced many factory workers. As we face the next step of the industrial revolution with the development of Industry 4.0 and smart robots, a massive period of technological unemployment could begin. If you are interested more about this topic visit intellipaat.com Machine Learning Online Course.
What is Industry 4.0?
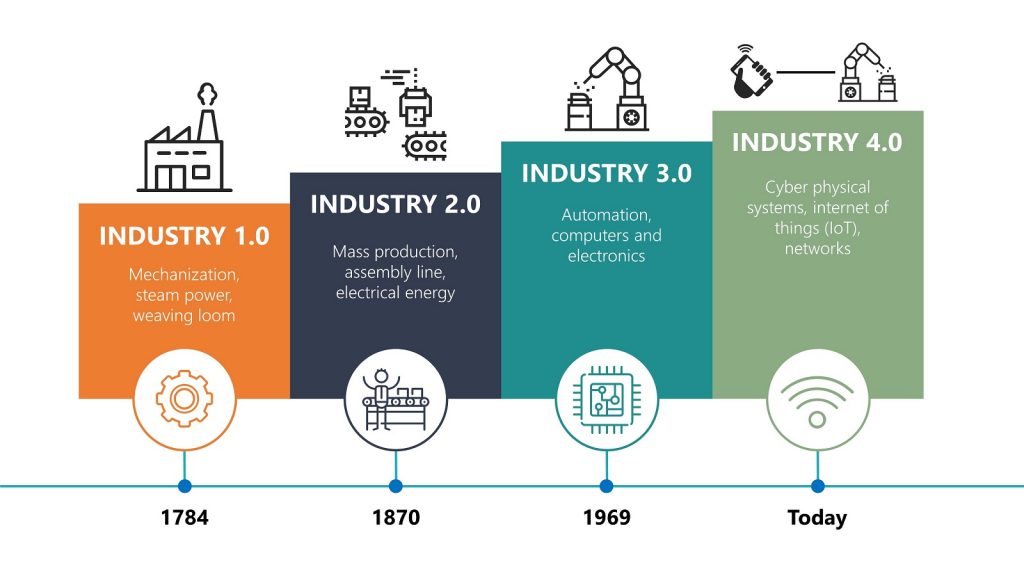
Industry 1.0 brought machines running on water power and steam energy and enabled higher production. 2.0 brought the assembly line. 3.0 brought industrial robots that were specialized in one specific task to limit redundant jobs.
According to Rozum, these complex robots use technological advances such as an increase in servo accessibility to accomplish these jobs with high speed and extreme precision. Industry 4.0 is bringing the next generation of interconnected robots. These robots will lead to an era of decentralized, collaborative production, with limited human interaction.
These new robots produce a huge amount of real-time data known as “Big Data” while running their processes. This data can be analyzed by humans in real-time to identify ways to constantly improve performance and allow predictions to limit downtime. For smaller companies, industry 4.0 will lower the cost to set up and operate robots. The new machines can be configured to perform multiple jobs in multiple volumes. One can complete an entire process quicker and with a higher quality output than a whole assembly line of older machines.
Improvements within Industry 4.0
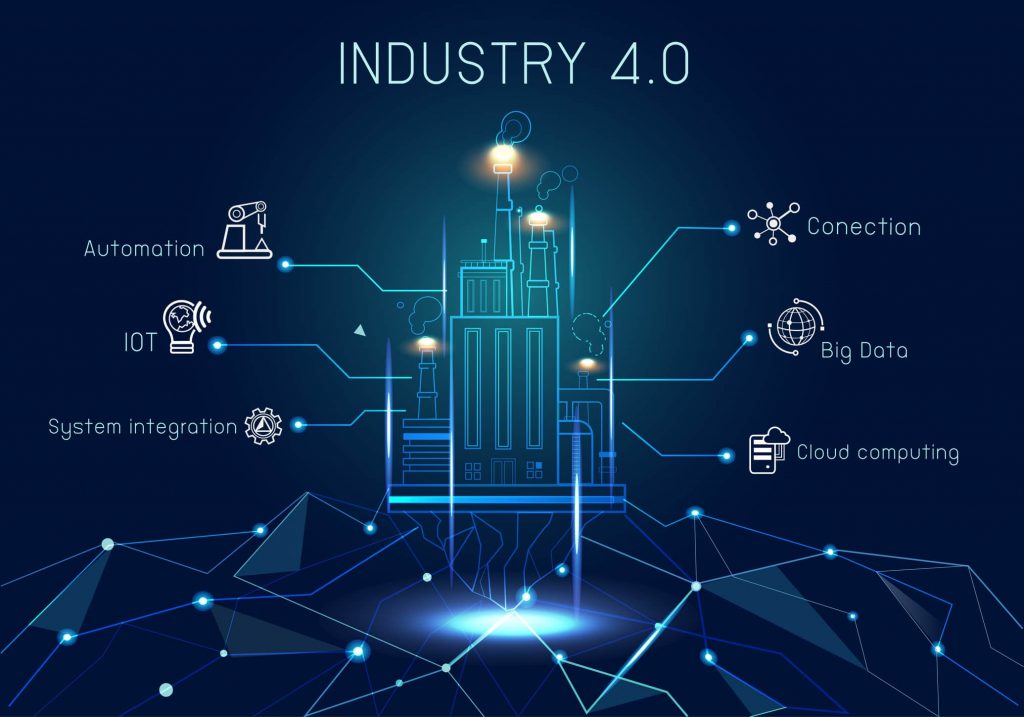
Companies are developing a process known as deep learning for industry 4.0 devices. Deep learning is similar to big data analysis except for the machine itself makes adjustments to the process. Deep learning technology was limited by the processing power and speed of the computers powering it.
The development of a microchip called a Graphical Processing Unit (GPUs). These chips allow huge amounts of data to be processed in seconds. This processing speeds allow artificial intelligence to teach itself how to run without human input. The capability of these machines is still limited but many companies are working on improving them.
What does this mean for human jobs?
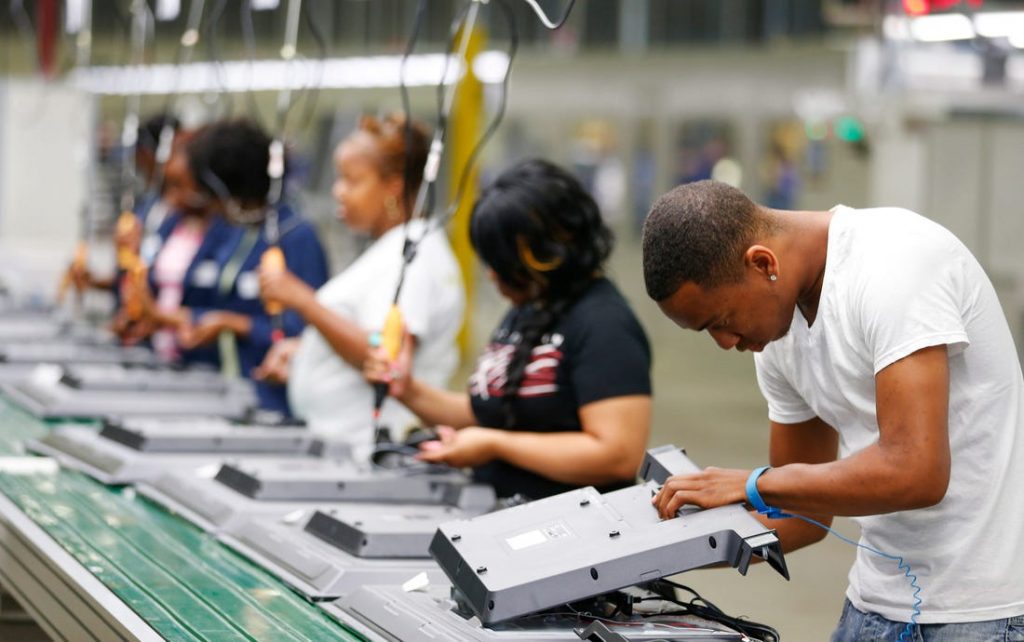
These machines will provide a more cost-effective way to manufacture high-quality products and will allow companies to be more competitive. These robots will be able to understand what they are meant to do but are still extremely far from thinking like a human. Until then, there is still a need for human input and jobs.
With the machines being able to make decisions on their specific jobs and monitoring the quality of the work they do, humans will be able to focus more on tasks that need critical thinking and more complex conditions. It could also improve the quality of human jobs being performed by eliminating redundant tasks.
Another way the industry may go is eliminating human jobs quicker than other sectors can create them. This could be supplemented through things like taxing production to supplement humans’ incomes.
Either of these options could happen but it is too early to tell. It is important to remember the impact that technology has on human jobs as manufacturing progresses to industry 4.0. Through all past industrial and technological advances, humans have not only survived, they thrived and produced higher quality parts for cheaper prices to consumers. As society advances, manufacturing has to advance with it.